Problems during Application and Marking
Problems can occur in the application and marking process, such as inaccurate adhesive application and incorrect marking due to ink splattering during printing. While the causes can vary from machine action timing to the surface tension or chemical affinity of adhesive and ink, static electricity can also cause problems during application and marking.
This section explains how problems during application and marking occur due to static electricity and possible solutions for these problems.
How problems during application and marking occur
Application and marking problems are caused by Coulomb forces. Coulomb force is a force of attraction between positive and negative charges and a force of repulsion between charges of the same polarity. The problems that occur differ according to which direction the force is working.
Problems caused by Coulomb force attraction
For example, the problem of material not dripping on the targeted position is caused by Coulomb force attraction.
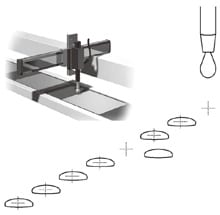
Let’s say that the material being applied is negatively charged when dripping. If the area around the dripping target position is positively charged, Coulomb force attraction works between that positive charge and the material being applied. The Coulomb force pulls at the material and causes it to drop to a position different from the target position.
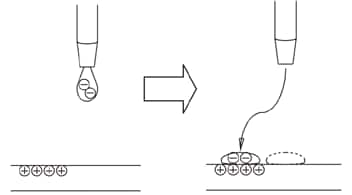
Problems caused by Coulomb force repulsion
For example, the problem of meandering sealant application is caused by Coulomb force repulsion.
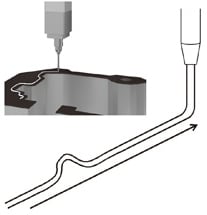
Let’s say that the materials are negatively charged before the application process. When the part to be painted is negatively charged, a repulsive Coulomb force works between the part and sealant being applied. What happens then is that the Coulomb force repels the sealant and causes the sealant to be applied away from the intended location.
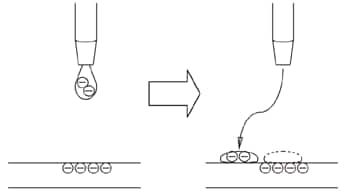
Measures for application and marking problems
Application and marking problems can be solved by making the Coulomb force disappear, which means to eliminate static electricity. While changing the material is one way to eliminate static, it is not easy to change materials in a manufacturing setting. Taking an appropriate anti-static measure for the target material is a better approach.
For example, using humidity control can be effective for paper, to allow electricity to flow easily. You can control Coulomb force by maintaining humidity within an appropriate range to allow static electricity to escape from the target.
However, for paper that is surface treated with plastic such as in rotogravure printing, or if the target is an insulator, humidity control is not as effective, and use of a static eliminator (ionizer) is more practical.
An ionizer to prevent application or marking problems is installed so that it aims at the tip of the nozzle. A nozzle-type ionizer is suitable for installing in narrow spaces.
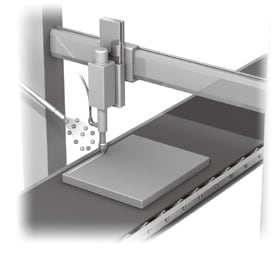